Metrc Compliance: Inventory Practices to Survive a Metrc Audit
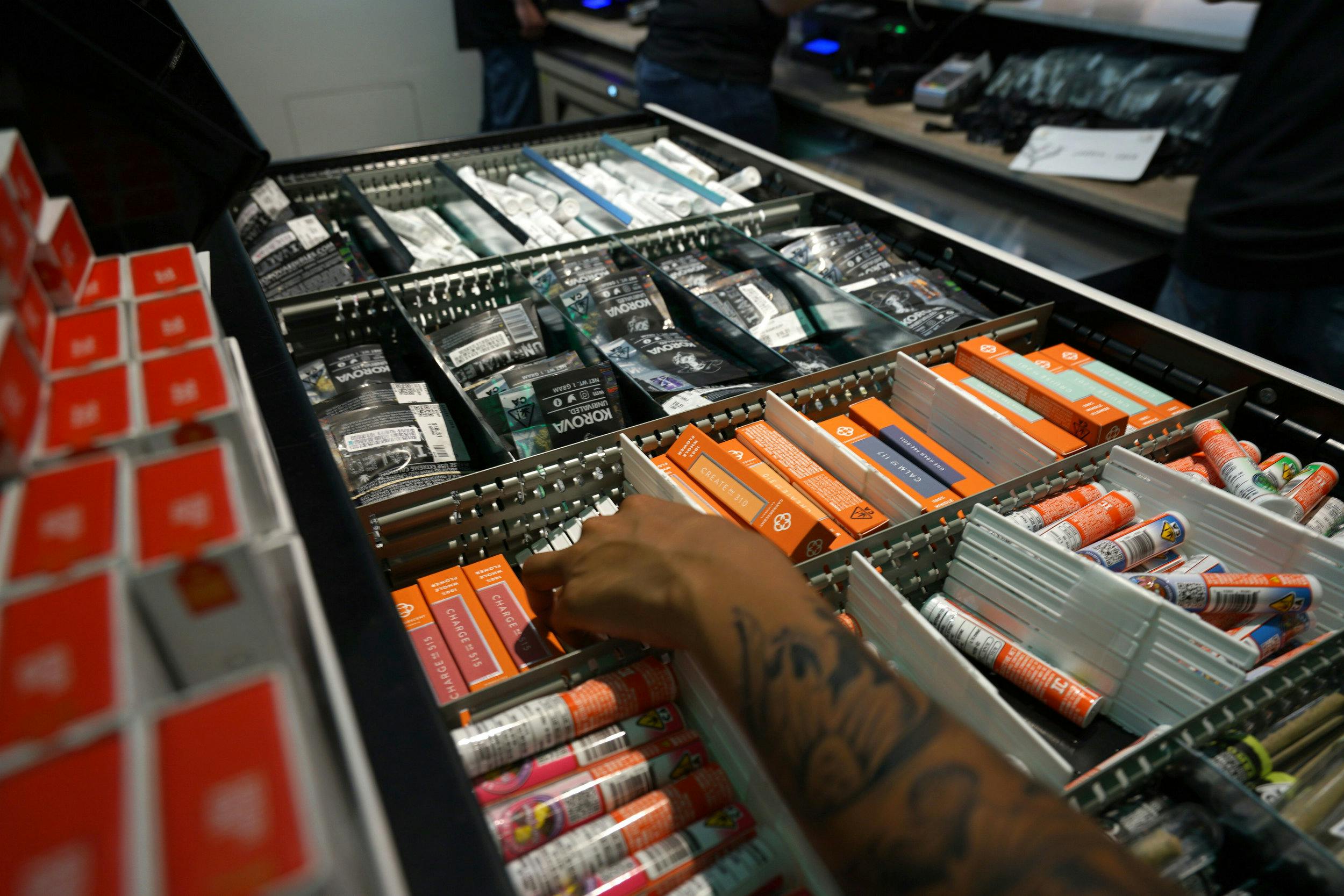
Over the past few months, California's Bureau of Cannabis Control (BCC) has been issuing annual licenses to industry operators throughout the supply chain. This means a couple of things:
- Metrc is no longer coming - it's here.
- It's time to master the art of inventory management.
In the new age of government cannabis tracking, meticulous inventory management practices reign supreme. And if you're not well-prepared, Metrc can easily consume all of your time and attention... but it doesn't have to.
That's why we teamed up with Metrc compliance experts and inventory managers from some of California's largest dispensaries to bring together their tried-and-true strategies for methodical inventory organization and routine counting. By adopting these habits right now, you'll be armed with best practices that are second-nature to you and your staff, in addition to being prepared to thrive in a track-and-trace world, the moment your license is issued.
The 30 Day and 3% Rules: How Metrc Compliance Demands Exemplary Inventory Management
When you boil it down to the core, Metrc compliance requirements all center around how much inventory is where at any given time. In fact, California regulations on cannabis require you to complete a full inventory Metrc audit (more commonly referred to as 'counts') and submit reconciliations for any discrepancies at least once every 30 days. Meaning, submitting frequently inaccurate inventory counts (or forgetting to submit them altogether) is a sure-fire way to fall out of Metrc compliance.
This is why establishing a consistent, second-nature count process is one of the most significant components of maintaining Metrc compliance and is paramount to your success. However, these Metrc audits also provide a valuable opportunity for you to see how precise your inventory management is on a regular basis. And patterns in discrepancies can be used to pinpoint opportunities for improvement in your inventory intake, organization, selling, or counting methods. We'll go into more on that soon...
This 30-day inventory Metrc audit requirement exists so the BCC can monitor the results of your count. If your inventory count has a variance greater than 3% of your average monthly sales, the state considers that a 'significant discrepancy' which could flag your license for an audit or penalties. A variance of 3% isn't very forgiving and if you're not careful, it's easy to accumulate enough errors to add up to a significant discrepancy pretty quickly.
That's why top dispensaries and Metrc compliance advisors agree that performing full counts and reconciliations must be part of your standard weekly procedures. Because they allow you to keep a close eye on all your inventory before any discrepancies or errors spin out of control. After all, the more time allowed between counts means a larger window of time for discrepancies to occur that you'll need to investigate and get to the bottom of. Since we know this can be a difficult and time-consuming process, here are our expert's 3 favorite ways to tighten up your inventory management practices.
Inventory Management Practice #1: Separation
An easy rule of thumb to follow when organizing your inventory is, "How will I go about counting these?" By doing this, you're actually deliberately planning how every single unit is being organized and tracked internally. Though it might be tempting to combine different sizes, flavors, or shipments of a product for space reasons, you'll need to separate them out when the time comes to perform an inventory count. Thinking past the tedious sorting, Metrc stock counts are by package not by product - so combining different shipments is a one-way ticket to non-compliance, as you'll be unable to discern which units are from which batch.
Inventory Management Practice #2: Seals
To maximize the integrity of your inventory during storage, seal the boxes by taping them shut and writing the count, date, and your initials where the two ends of tape overlap - similar to how a tamper-proof seal works. If your dispensary software supports printing batch labels, stick these on the outside of the boxes to provide additional information about the contents (like product name, SKU, expiration date, etc.) so they don't need to be opened to know exactly what's inside. Additionally, stocking up on clear plastic boxes will let you see what goodies are inside at a glance, improving transparency and accountability, making it faster to double-check your compliance with Metrc stock requirements. You can keep them sealed individually at the box level like this, or move them into a locked/inaccessible location for additional assurance that they won't be touched.
Inventory Management Practice #3: Timely Entry
Keep inventory adjustments well-documented and easy to reference. Ideally, enter them into your dispensary software as they occur or as part of your end-of-night procedures, so the information is saved in a centralized location. This habit will make it much easier to identify the reasons for count discrepancies instead of relying on memory or he-said-she-said during investigations into any issues with your Metrc stock checks. Some adjustments to make a note of display units, testing samples, spoilage or other issues requiring product destruction, and mismatches between what was recorded and what was sold (i.e. staff handed over a different quantity or product than what was on the receipt). By recording these actions, you're leaving a trail of inventory breadcrumbs allowing you to better identify the causes of discrepancies when counting.
Best Counting Practices to Start Adopting NOW
Why leave practice to the last minute? Accurate counts ensure better reporting, cleaner bookkeeping, and proper management of your inventory. Plus, making them a habitual part of your dispensary's routine guarantees you'll be ready for the new Metrc compliance requirements out of the gate.
Counting Practice #1: Staffing
Select the staff members and train them on the counting process in advance so the team is ready to rock on count day. Employees who are detail-oriented, reliable, and familiar with your inventory are ideal for performing inventory counts. If you can, have the same employees do this task every time so you can save time on training and they can continue to improve their performance in this process. Also, designate a supervisor (such as an Inventory Manager, Team Lead, or Shift Supervisor) to manage employees and field issues that arise during the counting process - a single point of contact reduces inconsistency and confusion and cuts down on the chances of a tough Metrc audit in your future.
Counting Practice #2: Cycle Counts
This method entails counting a different segment (such as a brand or product type) of your inventory each day of the week, eventually cycling through all the products on hand. This quick practice allows you to keep a pulse on any discrepancies as they occur and reduces the downtime required when 'freezing' inventory for a complete count. This is an especially useful tactic for shops with a large number of SKUs, as it breaks the very time-consuming process of counting your shop's entire physical inventory into more manageable chunks - reducing the mental fatigue that would otherwise result in human error during a longer counting process.
Counting Practice #3: Pre-counts
Another valuable time-saving count strategy leverages similar tactics to the 'tamper-proof seal' storage method we mentioned above. Start by organizing stock into easily countable quantities (e.g. boxes of 25), and then set aside any stock that won't be needed until your scheduled count. Note the pre-count quantity, and when you're ready to perform your count, the inventory you set aside can quickly and easily be added to the count of stock on-hand. If you need to sell some of your pre-counted inventory, simply adjust the count of units wherever you recorded the pre-count figures.
You can make this process even more efficient by always storing your backstock inventory in sealed, batched amounts - exactly as is described in our 'Seals' section. Think about it this way: if you intake 100 units of a product, and typically sell ~25 units/week, you can create 4 batches of 25 units each, store them with a "tamper-proof seal," and only open a new batch after you've sold through the previous one. This means, when it comes time to perform a count, you only need to count the individual units from the open batch since you already know how many are contained in your sealed backstock batches. If you want to go a step further, you can even rubber band small items like cartridges, edibles, and extracts in groups of 5 (or another easy to count number) so you can quickly count consistent bundles as opposed to individual units. Easy, right?
Counting Practice #4: Double Counts
If time and personnel allow, double-count for optimal accuracy. Assign two employees to count the same products, but each should work independently from the other. When they're done with a count, compare each result before you make any adjustments. If there are any discrepancies and the reason for the variances aren't clear, repeat that product's count to ensure you record the correct number.
Counting Practice #5: The Right Tools
At the end of the day, managing your business is hard enough as is. Combine that with a quickly evolving regulatory landscape, ever-shifting timelines and a lack of information, and it's enough to make any operator's head spin! Luckily, there are a variety of modern software tools that retailers can leverage to help automate Metrc compliance, streamline inventory management and make their lives easier.
Enlisting the help of a cannabis-specific point of sale software system, designed to meet the demands of the industry is key. There are plenty of options to choose from, but which one is best for you will depend on a variety of factors, like whether or not your in a Track-and-Trace enabled state, the size of your business, and what type of licenses you hold. If Metrc (or another state system) is part of your operations, you need a platform that makes it easy for you to fulfill compliance requirements as part of your day-to-day activities. A platform like Treez arms operators with an inventory count page that makes counting easy and painless, a Metrc integration that allows you to automate your count submissions to the state, and most importantly: Knowledge and comfort knowing your dispensary software was created specifically for your compliance and workflows. Best practices can set you up for success, but a dispensary software built to support your execution of them give you an extra boost to help you over the Metrc compliance finish line.
Conclusion
Whether Metrc is here or not, it's high time your business reaped the benefits of these inventory management best practices. After all, it shouldn't require a government Metrc audit to see the value of increased accountability, fewer discrepancies, and more streamlined workflows.